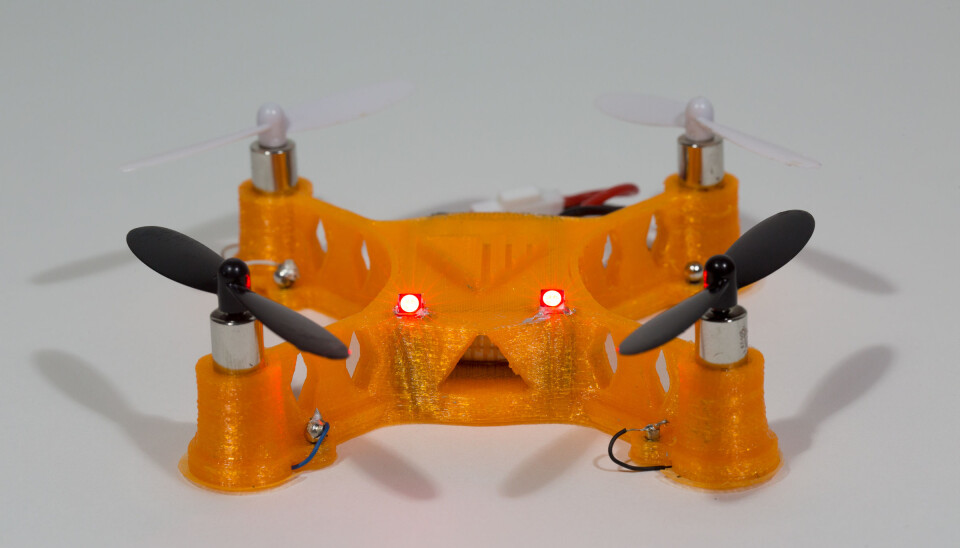
Snart kan du 3D-printe din egen elektronikk
Ny teknologi som kan 3D-printe med strømledende blekk gjør det mulig å lage elektronikk i én sammenhengende del. Metallrevolusjonen innen 3D-printing skjer nå.
Denne artikkelen er over ti år gammel og kan inneholde utdatert informasjon.
Har du lyst til å printe din egen drone? I løpet av året kommer en 3D printer på forbrukermarkedet som ikke bare kan skrive ut søte plastikk-dingser, men også elektronikk. Lag ditt eget design på en datamaskin, eller bruk et ferdigdesign du finner på nett og trykk «print».
Riktignok må du fortsatt gjøre en del ting manuelt, som å sette inn databrikke og montere rotorer. Men det nye med Voxel8 sin maskin, sammenlignet med andre forbruker-3D-printere, er at den har et eget sølvblekk som leder strøm. Dermed kan du integrere plastikk og strømledninger sømløst i én bit istedenfor å montere sammen mange forskjellige deler.
Men selv om det strømledende blekket åpner opp for mange nye muligheter for designere og entusiaster, er dette bare en smaksprøve på fremtiden.
Vi er nemlig midt i en revolusjon innen 3D-printing med metaller, som vil forandre måten vi produserer alt fra smarttelefoner til flymotorer.
Størrelsen teller
En av de største utfordringene med å 3D-printe rent metall er at det skal veldig høye temperaturer til for at det smelter. Og da kan det fort bli så store temperaturforskjeller mellom metallet og alt som er rundt, at når det blir kjølt ned, så vrir produktet seg.
Det strømledende blekket til Voxel8 er en slags flytende pasta av små sølvpartikler. Men resultatet er altfor grovt, på nesten 1 millimeter i tykkelse, til å virkelig kunne printe avansert elektronikk.
Nå har derimot nederlandske forskere fra Universitetet i Twente klart å 3D-printe rene gull- og kobberstenger som er mindre enn 5 mikrometer, altså tusendeler av en milimeter, tykke.
Å kunne 3D-printe så tynt med rene metaller kan åpne opp for produksjon av bittesmå elektroniske dingser. For eksempel vil det bli mulig å printe mikroskopiske koblinger mellom databrikker. De elektriske koblingene kan printes samtidig som materialet rundt, istedenfor å måtte lage et eget skall og så montere elektronikken inni etterpå.
Bittesmå elektroniske dingser
Claas Willem Visser er en av forskerne bak den nye metoden. Han mener det spesielle med den nye metoden er at de både klarer å printe syltynne og samtidig relativt høye metallstenger. Å kunne bygge i høyden, selv om det bare er snakk om opptil 2 millimeter, åpner nemlig for mange nye muligheter.
– Vi kan koble sammen databrikker vertikalt, forteller Visser om potensialet for teknologien.
Å kunne koble sammen todimensjonale databrikker lag på lag, vil kunne spare mye plass og forsterke koblingene og dermed signalene mellom brikkene.
Da er det bare fantasien som begrenser hva slags bittesmå elektroniske gjenstander 3D-printing kan bidra til å lage.
Som å stable pannekaker
De fleste 3D-printerne som er tilgjengelig for folk flest bruker samme tankegang som hjemmekontorprinteren, med forskjellig typer «blekk» som sprøytes ut av forskjellige dyser.
- Les også: Trenger du ting? Trykk print
Teknologien man kaller 3D-printing i industrien og forskning har derimot helt andre strategier for å lage ting i tre dimensjoner.
Siden metall krever høye temperaturer for å smelte, ville de fleste dysene som er tilgjengelige for vanlig 3D-printing rett og slett smelte.
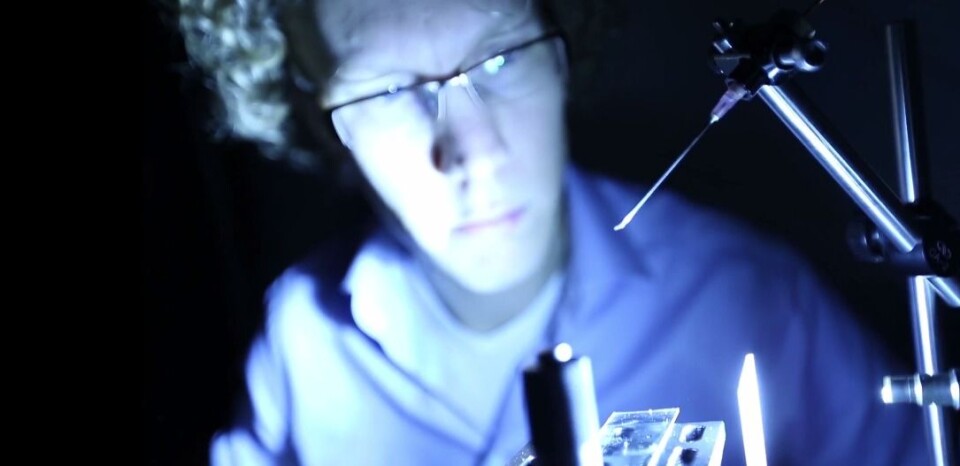
Visser og kollegaer bruker en dråpe-teknikk, såkalt LIFT (Laser-Induced Forward Transfer), hvor de stabler mikroskopiske metalldråper oppå hverandre. Maskinen skyter en syltynn laserstråle opp mot en plate dekket med et tynt lag med metall. I det punktet laserstrålen treffer, smelter en liten dråpe med metall som faller ned på en annen plate. Ved å bevege den øverste platen, kan de gjenta prosessen og dråpene blir stablet oppå hverandre til en tynn stang.
Dette er første gang noen har klart å bygge en stang av metalldråper ved bruk av denne teknologien. Visser forklarer de greier det ved å øke styrken på laseren, og det får dråpene til å falle raskere. Når dråpene treffer underlaget blir de klemt flate, og det gjør det lettere å stable dem oppå hverandre.
– Det er som å stable pannekaker istedenfor baller, forklarer Visser.
– Ser litt røft ut
Vegard Brøtan, som forsker på 3D-printing av metall ved NTNU og SINTEF, mener det spesielle med den nederlandske studien er hvor lite og tynt metallet blir. Likevel påpeker han at det fortsatt gjenstår en del før man kan ta denne teknologien i bruk.
– Det ser litt røft ut, selv om det er veldig lite, sier Brøtan om resultatene til Visser og kollegaer.
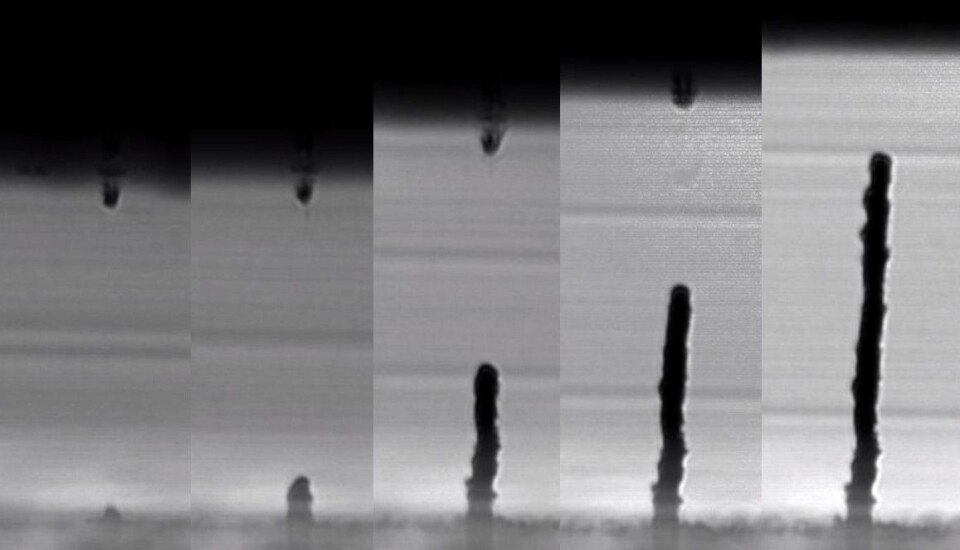
Han forteller også at det er mange anvendelser av 3D-printing med metall som ikke er avhengig av like tynt resultat, som for eksempel verktøy, medisinske deler, gullsmedprodukter og deler til biler og fly.
- Les også: Skriver ut celler for å kurere blindhet
– Komplekse komponenter som er satt sammen av mange deler nå, kan lages som én del i fremtiden, forklarer Brøtan.
På denne måten slipper man sammenskruingen og kan spare både materialer og tid.
Raskere og billigere
Ved Sintef produserer Brøtan og kollegaer avanserte støpeformer av stål med 3D-printing, eller såkalt additiv teknologi. Støpeformene blir blant annet brukt til å lage bildeler.
Brøtan forklarer at det kan være mye penger å spare for bilprodusenter ved å bruke støpeformer laget på denne måten.
En del av hemmeligheten bak de 3D-printede støpeformene er de innebygde kjølekanalene. Bilindustrien i Norge bruker Sintef-bygde former til å støpe bildeler av både plast og metall. Disse støpe-materialene helles oppi formen, og for at de skal herdes effektivt må nedkjølingen skje raskt. Da må kjølekanalene i støpeformen være så nærme som mulig overflaten, der det varme støpe-materialet er.
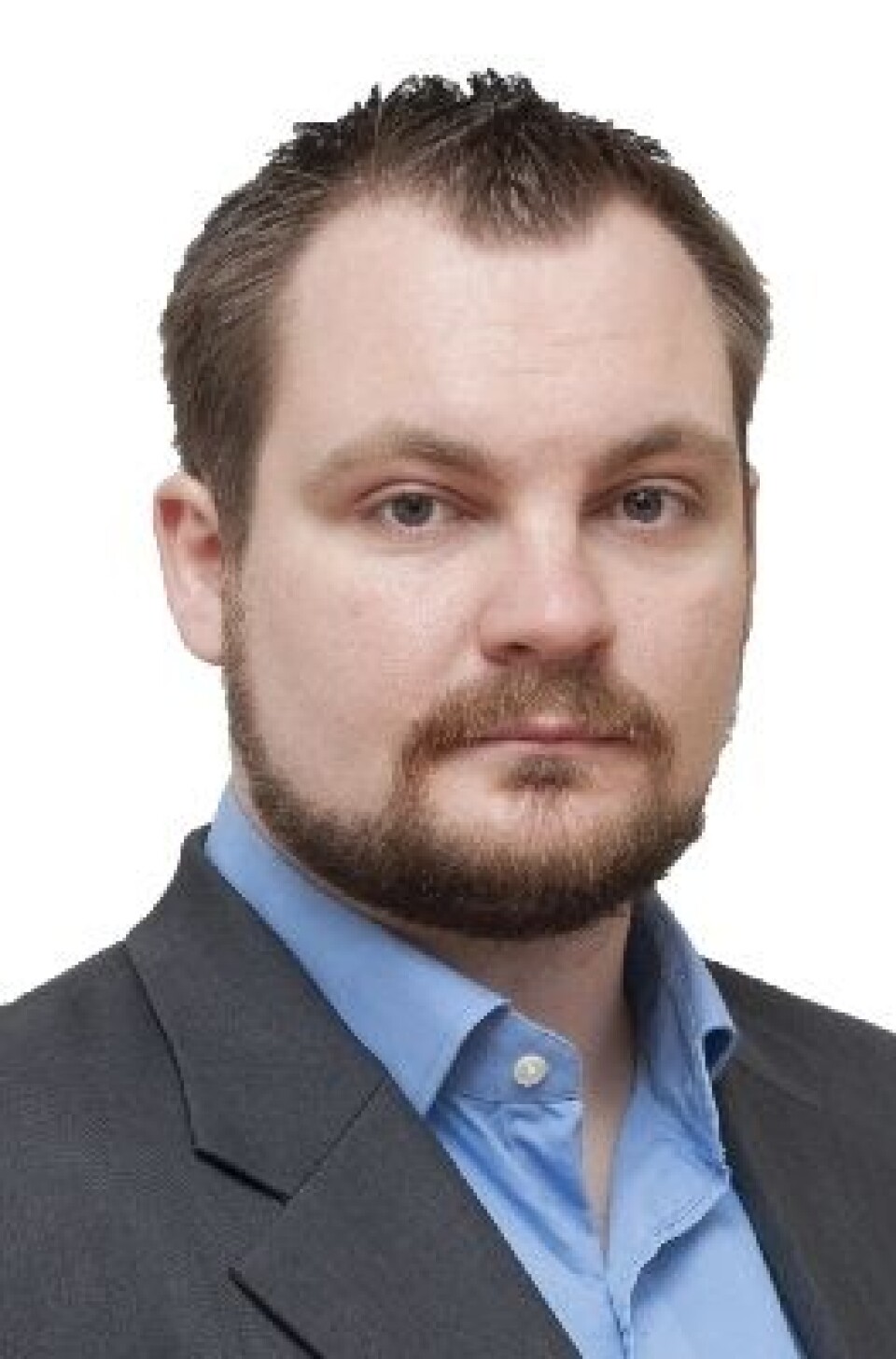
Med tradisjonelle metoder må kjølekanaler gjerne bores inn i støpeformen som rette hull. Det begrenser hvor tett inntil overflaten kjølingen kan skje. Men med 3D-printing blir kjølekanalene og selve støpeformen laget samtidig, som gjør det mulig å lage former man aldri kunne lage før.
– Det betyr at kjølekanalene kan følge tett inntil støpeformens overflate, uavhengig av geometri, forklarer Brøtan.
Bilindustrien har vært tidlig ute med å ta i bruk 3D-printing og står for 17 prosent av bruken slik teknologi internasjonalt. Men flyindustrien er hakk i hel og står for 12 prosent av den industrielle bruken av 3D-printing.
Verdens første 3D-printede jetmotor
For det er også mye penger å spare på å bruke 3D-printing i flydeler. Avanserte metalldeler, som vanligvis tar uker eller måneder å produsere, kan nå lages på noen få timer.
Og som et bevis på de teknologiske fremskrittene de siste årene, ble verdens første 3D-printede jetmotor avduket på et internasjonalt flyshow tidligere i år.
Jetmotoren er laget av australske forskere med additiv teknologi, som ligner på metoden Brøtan bruker på Sintef. Istedenfor å printe med flytende metall, starter prosessen med et tynt lag med metallpulver. En laser smelter metallpulveret etter designet som har blitt foret inn i maskinen. Dette skjer ett lag av gangen. Når ett todimensjonalt lag er ferdig, blir det dekket med nytt metallpulver, og laseren begynner på neste lag.
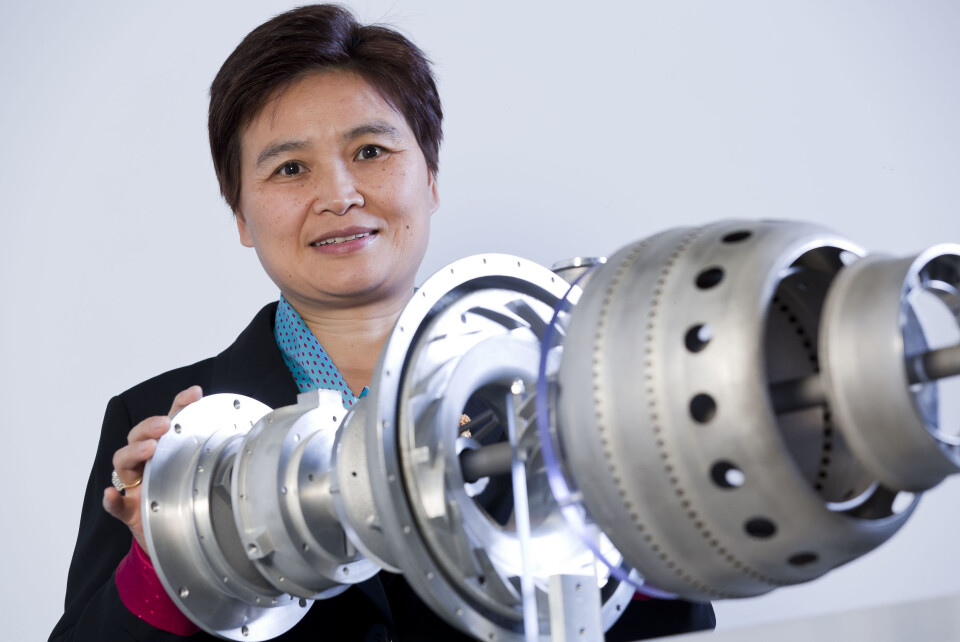
Resultatet blir en tredimensjonal metalldel, som kan være så enkel eller avansert som fantasien tillater – det har faktisk ingen betydning for prosessen.
Selv om den 3D-printede jetmotoren er en utstillingsmodell, er det flere flyselskaper som har meldt sin interesse til de australske forskerne.
Og det er ikke bare produksjonen av flydeler som blir mer effektiv. Ved å 3D-printe flydeler, kan flyene bli lettere. For eksempel vil 3D-printede drivstoffdyser som er laget i én del, istedenfor å bli satt sammen av 18 forskjellige deler, finnes i flere flymotorer i løpet av 2016, ifølge GE Aviation. Disse dysene skal være 25 prosent lettere og ha avansert kjøling innebygd, som fører til mindre bruk av drivstoff.
3D-printing kan altså spare både penger og miljøet.
Full kontroll i tre dimensjoner
Men vil smarttelefonen din være 3D-printet i fremtiden?
Visser mener at deres dråpe-metode har potensialet for å printe og teste nye elektriske kretser, men at den har sine klare begrensninger.
– De mest avanserte databrikkene som brukes i dag, for eksempel i smarttelefoner eller laptoper, krever oppløsning på rundt 10 nanometer. Vår teknikk er minst 100 ganger større, og derfor ikke egnet for slikt bruk, sier Visser.
Men selv om det enda ikke går an å printe tynt nok metall til å lage den mest avanserte elektronikken, kan allerede metalldeler printes med høy presisjon på mikrometernivå med kommersiell 3D-printing. Selskaper som Microfabrica og 3D MicroPrint printer små bevegelige metalldeler som ikke krever noen montering, og kan brukes i alt fra bilindustrien til medisinsk utstyr.
For disse selskapene er presisjon nøkkelen til suksess. Direktøren i 3D MicroPrint, Joachim Goebner, tror vi vil kunne 3D-printe elektronikk så snart en teknologi har full kontroll på hva den printer i alle tre dimensjonene.
– Da kan teknologien produsere nesten hva som helst, forteller Goebner.
Referanse:
Claas Willem Visser m.fl: Toward 3D Printing of Pure Metals by Laser-Induced Forward Transfer, Advanced Materials, juni 2015